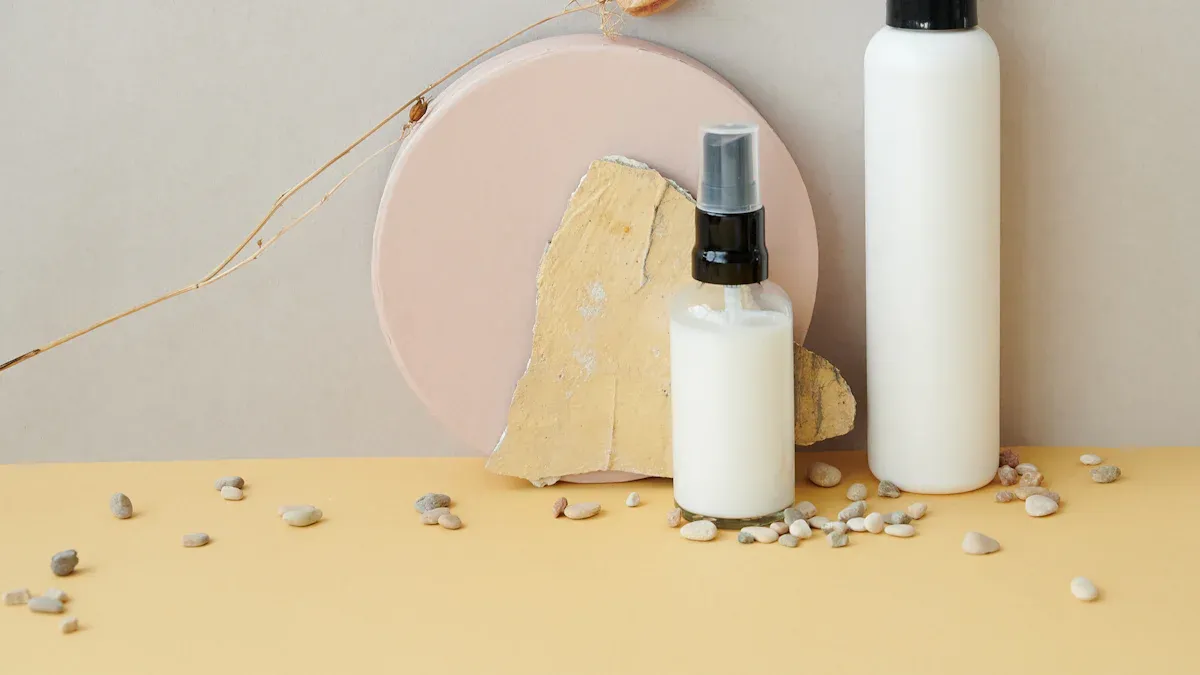
Reducing lead times in cosmetics production helps you stay ahead in a competitive market. Faster processes enable quicker innovation cycles, allowing you to meet customer demands with new products. By improving resource allocation and reducing waste, you can lower costs and offer competitive pricing. Rapid customization also strengthens brand loyalty as you respond to consumer preferences. Integrating research and development with production enhances agility, ensuring your business adapts swiftly to market changes while maintaining high-quality standards.
Advanced Technologies to Reduce Lead Times
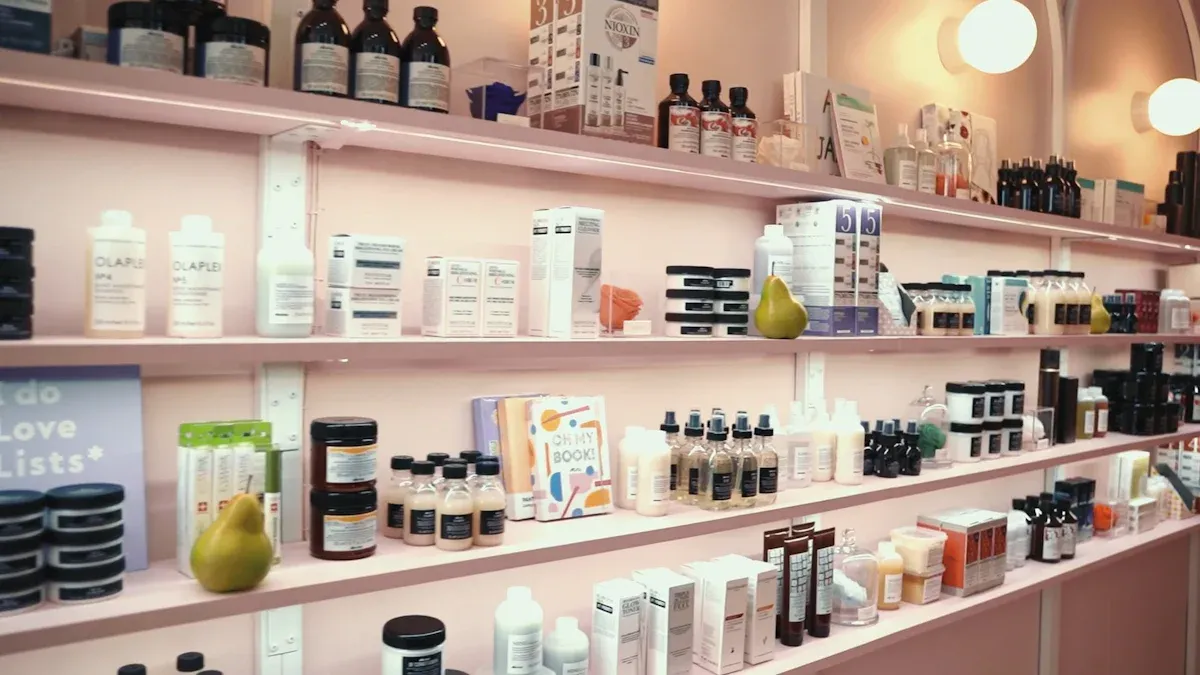
Automation and Robotics in Cosmetics Production
Automation and robotics are transforming cosmetics production by streamlining processes and reducing reliance on manual labor. Automated assembly lines and robotic systems can handle repetitive tasks with precision, ensuring consistent quality. For example, digital manufacturing creates a virtual production environment where you can identify and resolve issues early. This approach minimizes delays and shortens time-to-market. Automated machines also enhance production output, allowing you to meet high demand without compromising efficiency.
In Korea, a global beauty company has successfully reduced the lead time for launching new products by 50% through the integration of AI and 3D printing technologies. These advancements have also decreased production defects by 54%, showcasing the potential of automation to improve both speed and quality. By adopting similar technologies, you can achieve faster production cycles and maintain high standards.
Benefits of Smart Manufacturing Systems
Smart manufacturing systems combine advanced technologies like big data, process automation, and supply chain management to optimize cosmetics production. These systems enable real-time monitoring and data-driven decision-making, which can significantly reduce lead time. For instance, automated assembly lines and mass fabrication machines improve production speed while maintaining consistency.
Element | Impact on Manufacturing Performance (MP) | Impact on Sustainability (SM) |
---|---|---|
Manufacturing Big Data (MBD) | Positive and significant | |
Process Automation (PA) | Positive and significant | Positive and significant |
Supply Chain Integration (SCI) | Positive and significant | Positive and significant |
By leveraging these elements, you can enhance efficiency and sustainability in your operations. Smart systems also allow for seamless integration across departments, improving communication and reducing errors.
Scalable Technology Solutions for Efficiency
Scalable technology solutions play a crucial role in maintaining efficiency as your production needs grow. Advanced production machines, such as Microfluidizer® technology, enable the creation of stable nanoemulsions and liposomes with uniform quality across batches. This ensures consistency in large-scale cosmetics production while reducing waste.
Eco-friendly practices, such as energy-efficient machinery, further enhance efficiency by lowering costs and minimizing environmental impact. Improved team communication also prevents delays and errors, ensuring smooth operations. By adopting scalable solutions, you can meet increasing demand without sacrificing quality or speed.
Streamlining Quality Control for Faster Production
Real-Time Quality Monitoring Systems
Real-time quality monitoring systems help you identify issues immediately, ensuring faster decision-making and problem resolution. These systems provide constant visibility into factory performance, allowing you to detect anomalies as they occur. Operators can take corrective actions quickly, minimizing unplanned downtime and improving overall efficiency. For example, access to updated performance indicators enables managers to evaluate processes and optimize production workflows.
Evidence Description | Contribution to Faster Production Times |
---|---|
Constant visibility into factory performance | Quick identification of anomalies, leading to faster problem resolution. |
Immediate access to performance indicators | Reduces time needed to address issues, ensuring smoother operations. |
Quick resolution of problems | Minimizes downtime, enhancing factory efficiency and reducing lead times. |
By implementing real-time monitoring, you can streamline cosmetics production and maintain high-quality standards without delays.
Standardized Testing Protocols in Cosmetics Production
Standardized testing protocols ensure consistency and reliability in cosmetics production. These protocols help you maintain uniform quality across batches, reducing the need for rework. Metrics like first-pass yield (FPY) and overall equipment effectiveness (OEE) provide valuable insights into production efficiency. Tracking FPY helps you identify inefficiencies, while OEE data improves scheduling and machine utilization.
Metric | Description | How to Use It |
---|---|---|
Yield | Measures process effectiveness, including first-pass yield (FPY). | Track FPY to identify inefficiencies and optimize production efficiency. |
Overall Equipment Effectiveness (OEE) | A measure of productivity calculated as availability x performance x quality. | Use OEE data to improve scheduling and maximize machine utilization. |
Throughput | Quantity of goods produced over a specific period. | Analyze throughput to identify bottlenecks and set realistic production goals. |
Internal Timing Efficiency Metrics | Metrics like manufacturing cycle time and changeover time that indicate operational efficiency. | Monitor these metrics to improve timing and reduce delays in production processes. |
Adopting standardized protocols not only enhances quality control but also helps reduce lead time by eliminating inefficiencies.
Training Teams for Efficient Quality Assessments
Well-trained teams play a crucial role in maintaining effective quality control. By equipping your staff with the right skills, you can ensure faster and more accurate quality assessments. Training programs should focus on identifying defects, understanding testing protocols, and using monitoring tools effectively. This approach minimizes errors and ensures that production runs smoothly.
Regular workshops and hands-on training sessions keep your team updated on the latest quality control techniques. When your staff is confident in their abilities, they can quickly identify and resolve issues, preventing delays in cosmetics production. Investing in team training not only boosts efficiency but also strengthens your overall supply chain management.
Optimizing Production Layout to Reduce Waste

Designing Efficient Workflow Layouts
An efficient workflow layout improves how workers, materials, and equipment interact in cosmetics production. By strategically planning areas such as formulation, testing, and packaging, you can reduce unnecessary movement and enhance productivity. A well-designed laboratory layout minimizes risks like lost inventory and worker accidents while supporting smooth operations.
To optimize workflows, focus on eliminating waste types such as defects, overproduction, and waiting. Measurement tools like cycle time and throughput help you evaluate efficiency and identify areas for improvement. For example:
Streamlined processes reduce errors.
Optimized machine settings minimize material waste.
Holistic production views eliminate non-value-adding processes.
By implementing these principles, you can reduce waste and improve overall efficiency in your facility.
Eliminating Bottlenecks in Production Processes
Bottlenecks slow down cosmetics production and increase lead times. Identifying and addressing these issues ensures smoother operations. Strategic placement of equipment and materials streamlines the flow of workers and resources, reducing delays. Clear layout guidelines provide best practices for organizing the production floor, enhancing productivity.
Principle | Impact on Waste Reduction |
---|---|
Strategic placement | Streamlines flow of materials and workers, reducing delays. |
Enhanced productivity | Minimizes production costs and improves efficiency. |
Clear layout guidelines | Provides best practices for organizing the production floor. |
By focusing on these principles, you can eliminate bottlenecks and maintain consistent production cycles.
Lean Layouts for Space Utilization
Lean layouts maximize space utilization while reducing lead times. By reorganizing your production floor, you can achieve significant improvements in efficiency. For example, lean layouts have demonstrated a 70-90% reduction in lead times and a 40% improvement in required space utilization.
Evidence Type | Statistic |
---|---|
Lead Time Reduction | 70-90% reduction |
Space Utilization Improvement | 40% reduction in required space |
Manufacturing Space Reduction | 41% reduction for same volume |
Lead Time Improvement | From 20+ days to 2 days |
These layouts allow you to produce the same volume of cosmetics in less space, reducing waste and improving supply chain management. By adopting lean principles, you can create a more efficient and sustainable production environment.
Enhancing Communication to Reduce Lead Time
Digital Collaboration Tools for Manufacturing Teams
Digital collaboration tools improve communication and efficiency in cosmetics production. These platforms provide real-time visibility across the supply chain, allowing you to monitor operations and identify potential bottlenecks. For example:
Stakeholders can access up-to-date data, ensuring transparency and better decision-making.
Automated systems streamline routine tasks like order processing, reducing delays.
Tools like IoT and RFID offer instant updates on inventory and shipments, helping you maintain operational efficiency.
By adopting these technologies, you can align your team and partners, eliminate misunderstandings, and reduce lead time effectively.
Cross-Departmental Coordination Strategies
Strong coordination between departments is essential for reducing lead times. When teams work in silos, communication gaps can lead to delays and inefficiencies. To address this, you should implement strategies that encourage collaboration:
Schedule regular cross-departmental meetings to discuss progress and challenges.
Use shared digital platforms to centralize information and updates.
Assign team leads to ensure accountability and smooth communication.
These strategies foster a culture of teamwork, ensuring that everyone works toward the same goals. Improved coordination also enhances supply chain management, helping you meet production deadlines consistently.
Clear Communication Protocols for Efficiency
Clear communication protocols ensure that everyone understands their roles and responsibilities. This minimizes resistance to new processes and keeps your team aligned with overall objectives. To establish effective protocols:
Develop a communication plan that outlines goals and expectations.
Involve stakeholders early to address concerns and gain their support.
Provide training to equip employees with the skills needed for process changes.
Assign process champions to advocate for improvements and guide the team.
Open communication reduces disruptions during transitions and ensures that your team stays focused on reducing lead time. Keeping everyone informed about changes also strengthens your supply chain management practices.
Lean Manufacturing Practices to Reduce Waste
Identifying and Eliminating Waste in Cosmetics Production
Waste in cosmetics production can take many forms, such as excess inventory, overproduction, or inefficient processes. Identifying these issues is the first step toward improving efficiency. You can start by analyzing your production line to pinpoint areas where resources are underutilized. For example, tracking material usage helps you reduce excess inventory, while monitoring machine performance minimizes downtime.
Lean manufacturing principles focus on eliminating non-value-adding activities. By addressing waste, you not only improve production speed but also enhance supply chain management. This approach ensures that every step in your process contributes to delivering high-quality products efficiently.
Continuous Improvement for Faster Processes
Continuous improvement programs help you adapt to changing market demands while maintaining efficiency. These programs focus on refining processes, adopting new technologies, and enhancing operational practices. Below is a table showcasing successful programs in the cosmetics industry:
Description | |
---|---|
Digital Transformation | Enhances efficiency and resilience by adopting digital solutions for better visibility and decision-making. |
Technology Adoption | Utilizes advanced tools like AI and automation to improve analytics and operational processes. |
Continuous Optimization | Focuses on ongoing improvements in supply chain practices to adapt to market changes and enhance product quality. |
By implementing these strategies, you can accelerate production cycles and reduce lead times. Regularly reviewing your processes ensures that your operations remain efficient and competitive.
Standardizing Workflows for Consistency
Standardized workflows create a structured approach to cosmetics production, reducing errors and delays. When every team follows the same procedures, you achieve consistent results across batches. For instance, Beauty Pie adopted Asana to manage their product launch lifecycle. Before this, they struggled with unstructured workflows that caused delays.
Using customizable templates, they established a consistent structure for every launch. Each task was assigned to an owner, ensuring accountability and clarity. Real-time visibility into project milestones allowed teams to address potential delays quickly. These practices streamlined their production process and kept projects on schedule.
Standardized workflows also improve communication and collaboration. When everyone knows their responsibilities, you can avoid misunderstandings and maintain efficiency. This approach not only enhances product quality but also reduces lead times significantly.
Leveraging Data to Optimize Lead Times
Monitoring Key Performance Indicators (KPIs)
Tracking key performance indicators (KPIs) helps you measure and improve the efficiency of your cosmetics production. KPIs like production cycle time, first-pass yield, and order fulfillment rates provide valuable insights into your operations. By monitoring these metrics, you can identify inefficiencies and take corrective actions to reduce lead time. For example, tracking production cycle time allows you to pinpoint delays in the manufacturing process. Similarly, monitoring first-pass yield helps you minimize rework by ensuring quality standards are met on the first attempt.
Using dashboards or software tools to visualize KPIs can make it easier to analyze trends and make data-driven decisions. These tools provide real-time updates, enabling you to respond quickly to any issues. When you focus on improving KPIs, you enhance supply chain management and ensure smoother operations.
Predictive Analytics for Demand Planning
Predictive analytics uses historical data and machine learning to forecast demand accurately. This approach helps you align production schedules with market needs, reducing excess inventory and avoiding stockouts. Companies like PepsiCo, L’Oréal, and 3M have successfully implemented predictive analytics to improve their demand planning processes. By leveraging this technology, you can optimize inventory management and reduce lead time.
A study shows that companies using machine learning for demand forecasting experience a 5-15% improvement in forecast reliability. This accuracy can reach up to 85-95%, ensuring that your production aligns with customer demand. Predictive analytics also allows you to anticipate seasonal trends and adjust your operations accordingly. This proactive approach minimizes waste and ensures that your cosmetics production remains efficient.
Improvement in Forecast Reliability | Percentage Increase |
---|---|
Companies using machine learning | 5 to 15 percent |
Forecast reliability | Up to 85-95 percent |
Adjusting Production Schedules Based on Data Insights
Adjusting production schedules based on data insights ensures that your operations remain flexible and efficient. Real-time data allows you to identify bottlenecks, optimize machine utilization, and prioritize urgent orders. For example, companies implementing Just-in-Time (JIT) production methodologies have achieved a 20-50% reduction in lead times. Reducing batch sizes, a key principle of JIT, further shortens lead times without compromising processing speeds.
By analyzing data trends, you can also predict potential disruptions and plan accordingly. This approach improves supply chain management by ensuring that resources are allocated effectively. When you adjust schedules based on data, you enhance overall productivity and maintain consistent delivery timelines.
Benefits of adjusting production schedules:
Shorter lead times through JIT methodologies.
Improved resource allocation and machine utilization.
Enhanced flexibility to meet changing market demands.
Data-driven scheduling not only boosts efficiency but also strengthens your ability to adapt to market fluctuations. This ensures that your cosmetics production stays competitive and responsive.
Strategic Partnerships for Faster Turnaround
Benefits of Domestic Suppliers in Reducing Lead Times
Partnering with domestic suppliers can significantly improve your production timelines. Local suppliers offer faster delivery times compared to international ones, reducing delays caused by customs or long shipping routes. For example, XYZ Cosmetics achieved remarkable results by collaborating with nearby suppliers and using a cloud-based platform for real-time data sharing. This approach not only minimized stockouts but also streamlined their operations.
You can also adopt Collaborative Planning, Forecasting, and Replenishment (CPFR) strategies. These methods synchronize efforts between suppliers, manufacturers, and retailers, ensuring better inventory management. By aligning your production needs with local suppliers, you can reduce lead times and enhance overall efficiency in cosmetics production.
Consolidating Suppliers for Timely Deliveries
Consolidating your supplier base simplifies operations and ensures timely deliveries. Fewer suppliers mean fewer points of contact, which reduces the complexity of managing your supply chain. Strategies like demand forecasting and Just-In-Time (JIT) inventory can further optimize your processes. For instance:
Demand forecasting uses historical sales data to predict future needs, such as increased sunscreen demand in summer.
JIT inventory ensures raw materials arrive just before production, minimizing storage costs.
Vendor-Managed Inventory (VMI) allows suppliers to maintain stock levels, ensuring a continuous supply without overstocking.
Freight consolidation is another effective strategy. By combining shipments from multiple suppliers, you can cut transportation costs by up to 30% while improving delivery efficiency. Centralized inventory management also enhances order accuracy and reduces turnaround times.
Incentives for Supplier Efficiency
Encouraging supplier efficiency benefits both parties. Offering incentives like performance-based bonuses or long-term contracts motivates suppliers to prioritize your orders. Advanced analytics tools can help you monitor supplier performance in real time, ensuring they meet agreed-upon standards.
You can also establish clear expectations through service-level agreements (SLAs). These agreements outline delivery timelines, quality standards, and penalties for non-compliance. When suppliers understand your priorities, they are more likely to align their processes with your goals. This proactive approach strengthens your supply chain management and ensures faster turnaround times.
Metric | Description |
---|---|
Time to Market | Collaborations can speed up product launches and market entry, enhancing operational efficiency. |
Supply Chain Metrics | Metrics like lead time reduction and cost savings are crucial for evaluating the effectiveness of partnerships. |
By fostering strong partnerships and offering incentives, you can build a reliable network of suppliers that supports your production goals.
Oully’s Approach to Reducing Lead Times
Fast 74-Day Production Turnaround
Oully sets a high standard in the beauty industry with its impressive 74-day production turnaround. This timeline includes every step, from initial concept development to final product delivery. By streamlining operations and leveraging advanced technologies, Oully ensures that your products reach the market faster. This rapid turnaround allows you to stay ahead of competitors and respond quickly to changing consumer demands.
Oully achieves this speed by integrating efficient workflows and cosmetics manufacturing software into its processes. These tools help monitor production stages in real time, ensuring that every task stays on schedule. With this approach, you can launch new products without unnecessary delays, giving your brand a competitive edge.
Customizable Solutions for Cosmetics Production
Every beauty brand has unique needs, and Oully understands the importance of customization. Whether you require specific formulations, packaging designs, or product types, Oully offers tailored solutions to bring your vision to life. Their team of experts works closely with you to ensure that every detail aligns with your brand identity.
Oully’s facility supports a wide range of product categories, including body care, facial care, hair care, and men’s grooming. This flexibility allows you to expand your product line without compromising quality or efficiency. By offering low minimum order quantities (MOQs), Oully makes it easier for emerging brands to enter the market. This adaptability ensures that your production process remains efficient and aligned with your goals.
Sustainable Practices to Reduce Waste
Sustainability is at the core of Oully’s operations. The company employs eco-friendly production processes to minimize environmental impact while maintaining high-quality standards. Energy-efficient machinery, waste reduction strategies, and sustainable sourcing practices all contribute to a greener production cycle.
Oully also focuses on reducing material waste during manufacturing. By optimizing workflows and using advanced equipment, they ensure that resources are utilized efficiently. These efforts not only support environmental goals but also help you meet the growing demand for sustainable beauty products. Choosing Oully as your manufacturing partner allows you to align your brand with eco-conscious values, appealing to environmentally aware consumers.
Tip: Partnering with a manufacturer like Oully can help you achieve faster lead times while maintaining a commitment to sustainability.
Reducing lead times in cosmetics production is vital for staying competitive in today’s fast-paced market. By adopting advanced technologies and optimizing workflows, you can improve efficiency and meet customer expectations. Leveraging data-driven strategies further enhances your ability to adapt to market demands. Manufacturers like Oully showcase how combining speed, quality, and sustainability can create a winning formula. When you implement these practices, you position your brand for long-term success in the beauty industry.
FAQ
What is lead time in cosmetics production?
Lead time refers to the total time it takes to manufacture and deliver a product, starting from the initial order to the final shipment. Reducing lead time helps you respond faster to market demands and improve customer satisfaction.
How can automation help reduce lead times?
Automation speeds up repetitive tasks like filling, labeling, and packaging. It ensures consistent quality and minimizes errors. By using automated systems, you can increase production efficiency and meet tight deadlines without sacrificing product standards.
Why is real-time quality monitoring important?
Real-time quality monitoring allows you to detect and fix issues immediately. This reduces downtime and prevents defective products from progressing through the production line. It ensures smoother operations and faster delivery times.
How does Oully achieve a 74-day production turnaround?
Oully uses advanced technologies, efficient workflows, and real-time monitoring to streamline every production stage. Their customizable solutions and commitment to sustainability further enhance their ability to deliver high-quality products quickly.
Can sustainable practices impact lead times?
Yes, sustainable practices like reducing waste and using energy-efficient machinery can improve efficiency. These methods optimize resource usage, which helps you maintain faster production cycles while supporting environmental goals.
Tip: Adopting eco-friendly practices not only reduces lead times but also appeals to environmentally conscious consumers.